As you navigate the warehouse of the future, implementing mobile robot solutions is essential for optimizing operations and staying ahead in the competitive landscape. By exploring the benefits and types of mobile robots, planning for seamless integration, and prioritizing staff training and safety, you lay a solid foundation. However, the real game-changer lies in how you approach performance monitoring, maintenance strategies, and future scalability. These critical aspects will not only boost efficiency today but also pave the way for sustained success in the ever-evolving world of warehouse logistics.
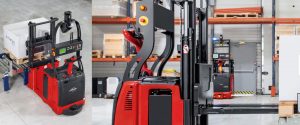
Benefits of Mobile Robots
Mobile robots in warehouses offer a myriad of advantages, enhancing efficiency and productivity in the logistics operations. By automating tasks like picking, sorting, and transporting goods, these robots optimize workflow, reduce human error, and increase throughput. Real-time data collection and analytics further improve decision-making processes, leading to streamlined operations and cost savings. Embracing mobile robots in warehouses is a strategic move towards a more competitive and agile supply chain.
Types of Mobile Robots
To understand the operational dynamics of modern warehouses fully, it is imperative to categorize and comprehend the diverse types of robots employed in these environments. Mobile robots can be classified into autonomous mobile robots, automated guided vehicles (AGVs), collaborative robots (cobots), and automated storage and retrieval systems (AS/RS). Each type offers unique features and functionalities that cater to specific warehouse requirements, optimizing efficiency and productivity.
Planning for Implementation
When strategizing for the implementation of mobile robot solutions in warehouses, thorough planning is essential to guarantee seamless integration and maximum operational efficiency. Consider factors like warehouse layout, inventory management systems, and peak operation hours. Conduct a detailed analysis of current workflows to identify areas for improvement and determine the most suitable tasks for mobile robots. This data-driven approach will secure a successful implementation process.
Integration With Existing Systems
For seamless integration with existing systems in warehouses, consider conducting a thorough review of your current technology infrastructure and operational processes. Identify potential points of integration with mobile robot solutions. Evaluate compatibility with warehouse management systems (WMS), enterprise resource planning (ERP) software, and other automation tools. Confirm data exchange protocols align with existing systems to optimize efficiency and minimize disruptions during implementation. Prioritize seamless connectivity to maximize the benefits of mobile robots.
Staff Training and Support
Effective implementation of staff training and support is vital for optimizing the utilization of mobile robot solutions in warehouses. Providing thorough training programs guarantees efficient operation and maintenance of the robots. Regular support and troubleshooting assistance empower staff to handle issues independently, reducing downtime. Continuous education on updated technologies and best practices enhances performance and promotes a culture of innovation within the warehouse environment.
Safety Considerations
To guarantee the safe operation of mobile robot solutions in warehouses, a thorough evaluation of potential hazards and the implementation of suitable safety measures are essential. Utilize sensors to detect obstacles, establish clearly marked robot zones, and make sure emergency stop mechanisms are in place. Regular safety audits and employee training on safety protocols are vital. Prioritize safety to mitigate risks and create a secure working environment for all warehouse operations.
Performance Monitoring
Implementing real-time data analytics is essential for tracking and optimizing the performance of mobile robot solutions in warehouses. By monitoring key metrics such as order fulfillment rates, travel time efficiency, and pick accuracy, you can identify areas for improvement and enhance overall operational efficiency. Utilizing performance monitoring tools allows you to make data-driven decisions, increase productivity, and streamline processes to meet the demands of a dynamic warehouse environment.
Maintenance and Upkeep
Regular maintenance schedules are essential for ensuring the peak performance and longevity of mobile robot solutions in warehouses. Implementing proactive maintenance routines based on manufacturer guidelines can prevent unexpected downtimes and costly repairs. Regularly checking sensors, motors, wheels, and batteries is vital for peak functionality. Utilizing data analytics to predict maintenance needs can further streamline operations and maximize the efficiency of mobile robot fleets.
Scalability and Future-proofing
Maintaining peak performance and longevity through proactive maintenance routines sets the foundation for considering scalability and future-proofing mobile robot solutions in warehouses. Scalability involves evaluating the system’s ability to adapt and grow with changing demands. Future-proofing requires anticipating advancements and ensuring flexibility for integration. By strategically planning for scalability and future needs, warehouses can optimize efficiency and stay competitive in the dynamic landscape of logistics.